When welding steel for use in materials handling and personnel operations, there is no greater concern than that of safety. One small flaw – even if it is too small to see – can be dangerous. This is why ethical practice demands that every lifting weld point should be tested, and this is why International Standards such as the ISO 9934 series guide the different ways this should be done. Mag Particle Testing your Welds is an important aspect of this safety and weld testing.
The Safety Risks of Poor Welding
Did you know that in the ten years from 2004 to 2013, 359 workers died in the Australian construction industry because of work related causes?
You might remember that in September, 2018, a man was killed and two others were injured after a tub of concrete fell from a crane at a construction site in Melbourne’s east. The kibble of concrete fell into the pit. One worker was killed, others were injured, and two men working in the pit were submerged in concrete. It was a horrific accident and, in response, Union Leader John Setka uttered the words, “No one should go to work and die.”
Furthermore, in 2019, Weld Australia CEO Geoff Crittenden discussed the importance the role welding plays in public safety.
“The entire lifecycle of the welding process – from design right through to inspection – must consider all aspects that could affect weld quality, and therefore public safety.
The Australian steel industry has for many years also been issuing warnings about the safety standards of steel products including forklift and crane lifting equipment being imported from overseas.
Crane Lifting Products and Mag Particle Testing
The fact is that cranes and crane lifting attachments are essential and widely used for transferring goods in various industries. Tower cranes, mobile cranes, gantry cranes and overhead lifting facilities are engaged in Australian construction, manufacturing and marine industries. The use of cranes directly aids productivity and cuts timelines, yet the risk inherent in using cranes and crane lift attachments in complex operations is no joke. Crane accidents of any kind can and do result in catastrophic impacts on the safety of workers and the public.
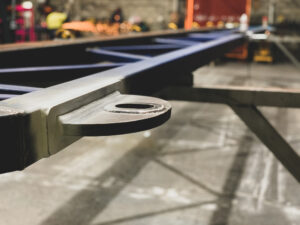
This is why it’s important that each and every product such as a lifting beam or a crane spreader beam features a welded crane-lift eye has Mag Particle Testing (MPI testing) done. And why a 100% pass is the only passing level that we will accept before our product will be approved for dispatch. All crane lift product that features welded lifting eyes, such as crane lifting cages, crane man cages, crane lift bins and even general crane attachments (such as pallet hooks, spreader beams, lifting beams and even crane bulk bag lifters) are all required to meet Australian Standards, and should all be provided with a compliance certificate demonstrating the MPI Test result that has been carried out in accordance with ISO 9934.
Mag Particle Testing
Magnetic particle inspection (MPI) testing of welds is a very effective form of surface-examination that aids in detecting surface and shallow subsurface discontinuities, or flaws, in ferromagnetic materials such as iron or steel. This is achieved in a non-destructive way that allows for visual inspections to quickly and efficiently detect any weaknesses in the weld, which can then be evaluated and rectified.
The seven most frequent welding defects are listed most commonly as:
- Cracks (these can be hot cracks, cold cracks, and crater cracks),
- Undercuts,
- Porosity,
- Incomplete fusion,
- Slag inclusion,
- Incomplete penetration, and
- Spatter
Through the process of MPI testing, each of these welding defects (if present) reveal themselves quickly and clearly to a precise location. The testing is completed by a qualified agent who effectively cleans the weld surface, magnetizes it, pours an iron powder over it, and then observes if and where the powder may gather. If a surface or slightly sub-surface defect is present, then lines of magnetic force will deform around it, causing the iron powder particles to bridge the gap caused by the defect and give an immediate visible indication.
This image below demonstrates flux lines flowing past both a perpendicular and parallel defect,
and flux leakage occurring around the perpendicular flaw. The presence of a surface or subsurface defect in the weld allows the magnetic flux to “leak” (since air cannot support as much magnetic field per unit volume as metals).
Whilst mag particle testing is only one of several forms of testing that may be completed, there are several obvious advantages to the practice. These include the efficient detection of both surface and subsurface defects, and that welds can be tested even if in difficult to reach or irregular locations on the product.
Always Choose Quality Australian Made Crane Lifting Attachments
Bremco Metal Products take great pride in the quality of our work, but we don’t just trust that our products look great. We ensure that mag particle testing is conducted on each and every crane lift attachment that we manufacture here in our Australian workshop. So if you purchase any Bremco product that features a wel
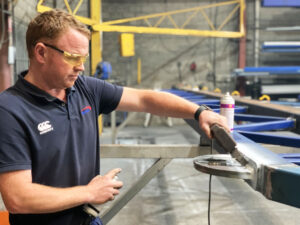
ded crane-lift eye, you will be issued a copy of the MPI testing results certificate demonstrating a 100% pass, meaning you and your workers can rest assured that you will all return safely to your families at the end of the day.
Every Bremco crane lift product that features welded lifting eyes, such as crane lifting cages, crane man cages, crane lift bins and general crane attachments (such as pallet hooks, spreader beams, and even crane bulk bag lifters) are all tested as part of our quality assurance practices, and every tested unit is provided with a compliance certificate demonstrating the MPI Test result that has been carried out in accordance with ISO 9934.
You should expect nothing less!